Supply Chain & Logistics of Medical Supplies
United States’ Procurement Offices
THE CHALLENGE
When the Covid 19 crisis hit the United States, many USA based manufacturers pivoted their facilities not for their own survival, but importantly they changed their production focus to support the World-Wide pandemic’s need for state-side manufactured Personal Protection Equipment (PPE). In particular disposable and reusable medical gowns were in dire need, and ordered for manufacturing by US state entities, along with the federally operated: Defense Logistics Agency (DLA) from a California based factory.
Temescal Creative, alongside this USA factory (who had re-tooled their entire facility to manufacture medical gowns) worked directly with US State procurement offices and the Defense Logistics Agency to supply their PPE needs.
In particular, the Defense Logistics Agency required all of their reusable gown manufacturing, to be 100% USA Made, also known as ‘Barry Compliant'. As a result Temescal Creative was responsible for sourcing all this Barry Compliant raw material and coordinating its yield requirements per production needs and delivery dates.
Daily interface between the factory’s in-house production team, their quality controls and shipping details was managed by Temescal Creative. The supply chain and logistics, such pallet sizing, carton sizes, units per box and all internal and external paperwork that required by each Distribution Center, was also managed and overseen by Temescal Creative.
Every single shipment went through strict quality control processes by this California Based factory. Over 2 million gowns and over 5 million additional medical supplies shipped across the United States and successfully delivered to help those in dire need.
Project Details
Role
Supply Chain Manager
Logistics Manager
Sourcing Coordinator
Client Relations
COLLABORATORS
LaLaLand Production & Design Factory


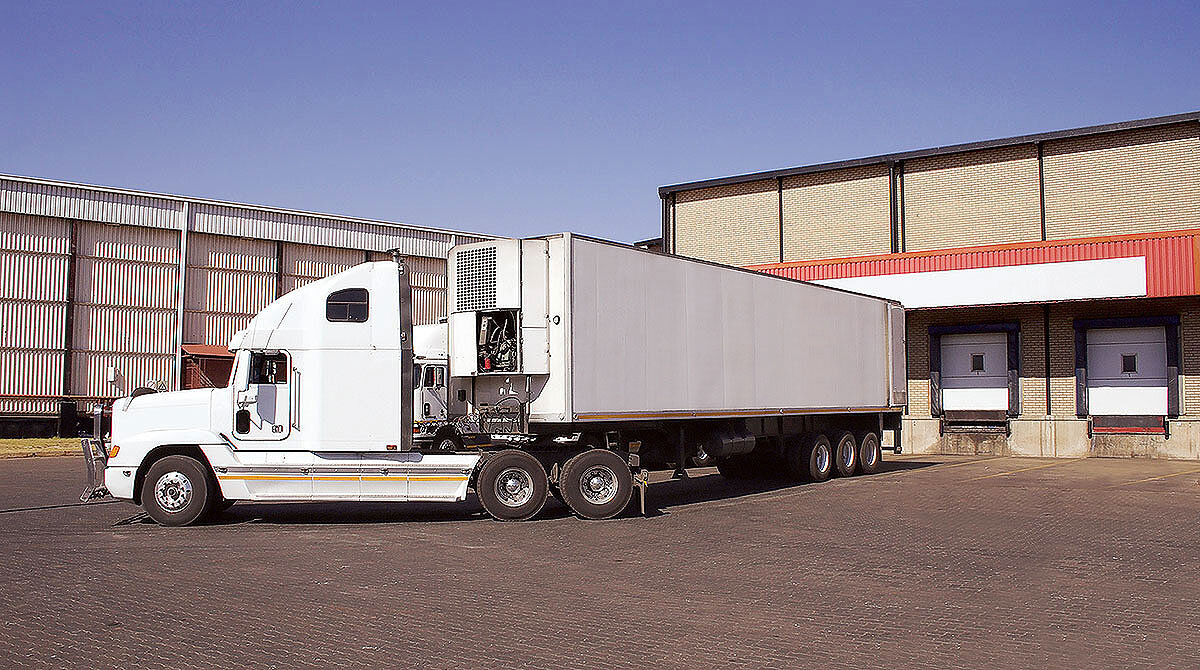

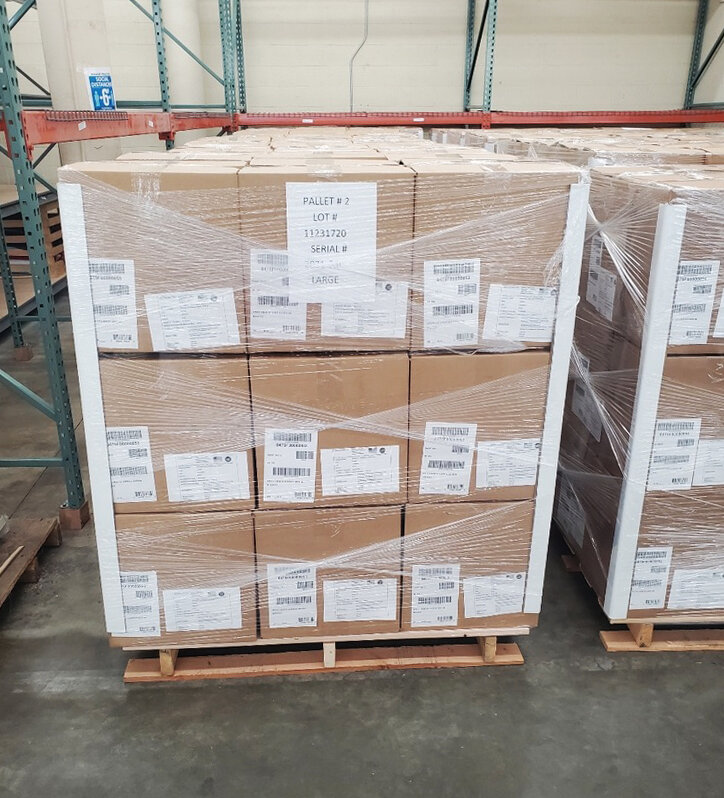
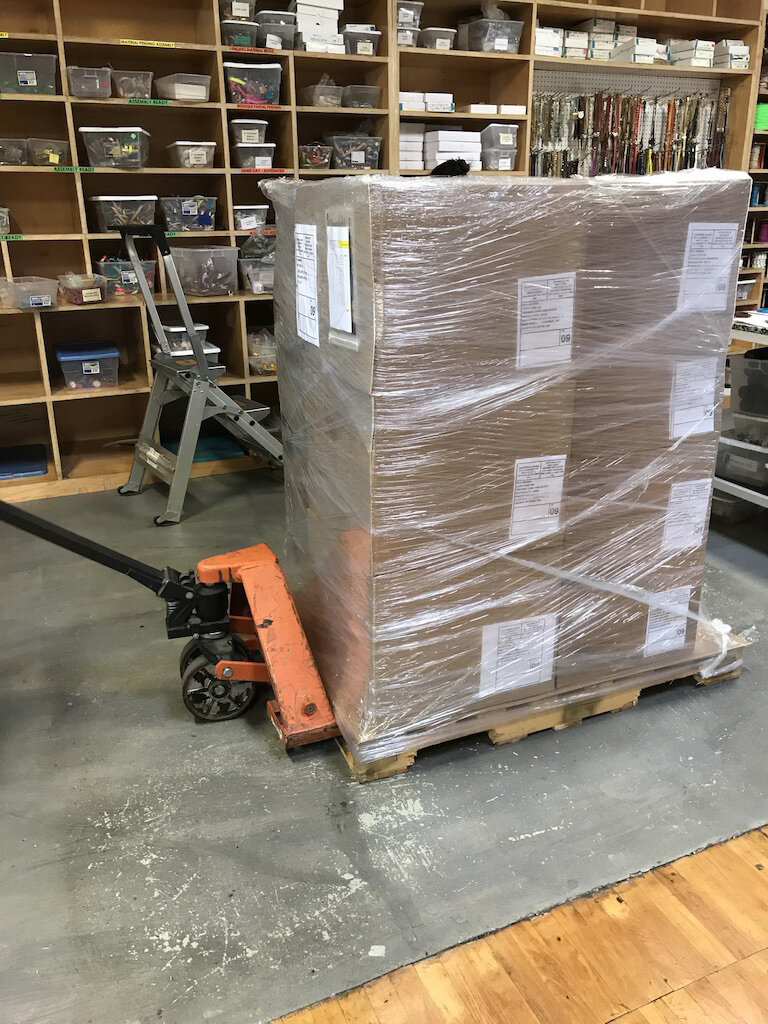

